Silicon dioxide (SiO₂) serves as a functional filler in semiconductor packaging, widely applied in both solid and liquid encapsulation technologies. Its primary roles include tuning thermomechanical properties, enhancing electrical performance, and ensuring material stability. As packaging technology advances, precise control over SiO₂ particle size, surface modification, and filler loading optimization becomes critical for improving reliability. This article explores the application mechanisms of SiO₂ in solid and liquid encapsulation, material design considerations, and provides a basic formulation reference.
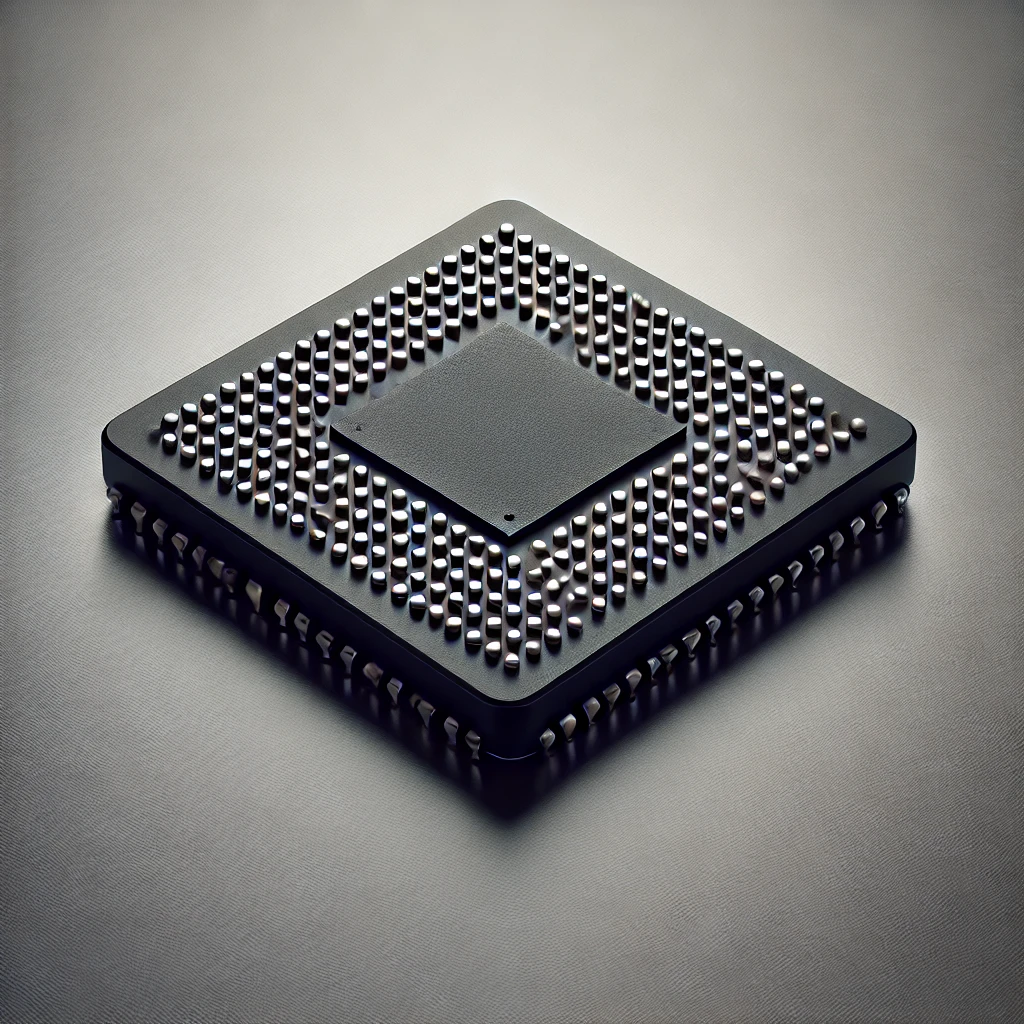
1. Application of Silicon Dioxide in Solid Encapsulation
Material Design and Functional Mechanisms
In solid encapsulation materials such as epoxy molding compound (EMC), SiO₂ is primarily used as a filler to adjust the coefficient of thermal expansion (CTE) and match that of the silicon die (CTE ≈ 2.6 ppm/°C), preventing thermal stress accumulation that could lead to die cracking. Additionally, appropriate SiO₂ loading significantly enhances mechanical strength and moisture resistance, further improving long-term package reliability.
In high-density packaging (e.g., BGA, QFN, CSP), SiO₂ particle size distribution and surface modification play a crucial role in molding performance and internal stress distribution. Typically, submicron SiO₂ (<1 µm) improves flowability and moldability but may compromise material rigidity, whereas mid-range particle sizes (2–10 µm) effectively lower CTE and enhance mechanical strength. Therefore, selecting the right filler size and loading depends on the specific application requirements.
Key Functions and Performance Optimization
- CTE Adjustment and Thermal Stress Control
- SiO₂ has a low thermal expansion coefficient (~0.5–1.0 ppm/°C), which helps reduce EMC CTE from 40–50 ppm/°C to around 10–15 ppm/°C, mitigating stress accumulation during thermal cycling.
- Mechanical Strength and Durability
- High SiO₂ loading (>60 wt%) significantly increases the modulus and hardness of encapsulation materials, preventing cracking under external stress or thermal load.
- Electrical Insulation and Reliability
- With its excellent insulating properties (dielectric constant ~3.9), SiO₂ effectively suppresses leakage currents and ensures signal integrity in high-frequency applications.
- Moisture Resistance and Long-Term Stability
- Surface modification of SiO₂ using silane coupling agents enhances compatibility with resin matrices, reducing moisture absorption and preventing interface delamination or conductive anodic filament (CAF) failures.
Typical Formulation
Component | Typical Ratio (wt%) | Function Description |
---|---|---|
Epoxy Resin | 25-35% | Provides base matrix, ensures molding properties |
Hardener | 5-10% | Promotes crosslinking reaction, affects mechanical properties |
SiO₂ Filler | 50-70% | Adjusts CTE, enhances rigidity and thermal stability |
Silane Coupling Agent | 1-2% | Improves filler-resin interface compatibility |
Additives (e.g., rheology modifiers) | 1-5% | Optimizes flowability and molding behavior |
2. Application of Silicon Dioxide in Liquid Encapsulation
Application Scenarios and Functional Mechanisms
Liquid encapsulation materials are primarily used for underfill, thermal interface materials (TIM), optical encapsulation, and conformal coatings. In these applications, SiO₂ not only helps control thermal expansion but also influences rheological behavior and optical properties, ensuring high encapsulation quality and long-term stability.
Key design factors for liquid encapsulation materials include SiO₂ particle size (affecting viscosity and flow behavior), surface modification (affecting dispersion stability), and filler loading (affecting mechanical and thermal properties). Depending on application requirements, either micron-sized SiO₂ (for improved modulus and thermal stability) or nanoscale SiO₂ (for enhanced optical clarity and flow properties) may be used.
Key Functions and Application Optimization
- Rheology Control
- SiO₂ acts as a rheology modifier, enabling shear-thinning behavior to reduce viscosity under applied stress, improving uniform filling and preventing void formation.
- Mechanical Strength and Reliability
- In underfill applications, SiO₂ enhances the modulus of the resin, reducing stress concentration between the die and substrate and improving package durability.
- Optical Property Adjustment
- High-purity SiO₂ is used in optical encapsulation (e.g., LED, optical MEMS) to match refractive indices, minimize internal reflection losses, and enhance light transmission.
- Thermal Expansion and Conductivity Control
- In TIM applications, SiO₂ loading reduces CTE while maintaining relatively low thermal conductivity, ensuring that packaging materials do not negatively impact overall heat dissipation performance.
Typical Formulation
Component | Typical Ratio (wt%) | Function Description |
---|---|---|
Epoxy/Silicone Resin | 10-20% | Provides base matrix, ensures flowability |
SiO₂ Filler | 75-90% | Adjusts CTE, influences rheological and mechanical properties |
Silane Coupling Agent | 0.5-1% | Enhances dispersion, improves interface compatibility |
Thixotropic Agent | 0-3% | Controls rheological behavior, optimizes dispensing performance |
Catalyst | 0.1-0.5% | Promotes curing reaction, enhances durability |
3. Conclusion and Future Outlook
Silicon dioxide plays a crucial role in both solid and liquid encapsulation, providing essential functions such as CTE control, mechanical reinforcement, optical tuning, and rheology adjustment. Depending on specific application needs, SiO₂ particle selection, surface modification, and filler loading must be optimized for maximum performance.
As advanced packaging technologies (e.g., 3D IC, FOWLP) continue to evolve, SiO₂ will play an increasingly diverse role in heterogeneous integration and high-reliability encapsulation, driving further innovation in material engineering.
Our company provides essential materials for the development of solid and liquid encapsulation. Feel free to contact us if you have any inquiries.
#SiliconDioxide #LowCTE #SemiconductorEncapsulation #Silica #SiO2 #LowDielectric #FOWLP #MechanicalStrengthEnhancement